ASHVILLE, NC—What happens when you take a couple of bike-geek
engineers accustomed to making precision robotics, high-end golf clubs and
medical equipment in a multi-million-dollar manufacturing facility and set them
loose designing bike components? In the case of Industry Nine, a new Asheville, North
Carolina, based components company, those engineers took a modest shot at
reinventing the wheel.
Industry Nine debuted at
Interbike last year with its unique new wheel design featuring an integrated
spoke-and-nipple design machined from a solid rod of 7075 T-6 aluminum. The
spokes thread directly into Industry Nine’s proprietary hub and can be used with
any 32-hole rim. Wheels can be trued with conventional spoke wrenches courtesy
of machined-in wrench flats on the nipple ends.
The bottom line for the rider is
fewer parts and—because it’s all aluminum—a lower rotational mass than even some
top competitors. In layman’s terms, that means you accelerate faster. The
process of milling each spoke from a solid bar of extruded aluminum takes about
two minutes per spoke on a quarter-million dollar lathe.
Industry Nine product manager
John Kiffmeyer said that using 32 spokes, laced to your choice of rim in a
tried-and-true two-cross pattern, makes the company’s wheels stronger than
comparably priced wheels that use forged aluminum spokes with a low-spoke-count,
direct-pull lacing pattern. The company offers stock price-point
wheelsets built with DT Swiss hoops in All-Mountain, Enduro, FR/DH, 29er and
Single Speed variations in three standard colors: anodized black, sliver or red.
Road and BMX wheels are in the works.
But don’t feel hampered by the
stock offerings—at Industry Nine customization is king. Spoke gauge, length and
spoke and hub color all can be made to order. Industry Nine’s
patent-pending spoke design is just part of the new company’s story. The company
is also waiting on a patent for a new freehub body drive mechanism that it
designed from the ground up. (Kiffmeyer said the company isn’t posting pictures
of the internals until the patent clears, so to see how one in action you have
to buy a rear hub and crack it open.)
The drive mechanism uses three or
six pawls, depending on preference, for engagement every six or three degrees of
rotation, respectively.
Whether the hub is set up with
the three- or six-pawl option, it is designed to only have three pawls engaged
at any given point. In addition to the hub’s quicker-than- average engagement,
each pawl has three engagement ridges, so there are always nine simultaneous
points of engagement. To ensure that all those tiny engagement points
stand up to even the angriest pedal mashers, the pawls and engagement ring are
cut from A-2 tool-grade steel with a process called Wire EDM (Electrical
Discharge Machining), an electrical erosion process that precision cuts
already-hardened steel to a tolerances within .0001 of an inch. Industry
Nine hubs have hardened stainless steel endcaps and 7075 aluminum hub shells and
axles. Freehub bodies are made from 7068 aluminum, an alloy with tensile
strength 25 percent greater than 7075. Wheelsets come with quick release or
thru-axle options, and the company now offers hub options for Cannondale Lefty
and Maverick fork users.
The only components the company
doesn’t fabricate on its own are rims and Japanese-made cartridge bearings—front
hubs get two, rear hubs get four. All that precision machining will set
you back about $850 per wheelset—a price point comparable to other
aluminum-spoked wheelsets but well worth it in terms of performance and the
ever-important “bling” factor. “We’re very aware of how important look
is, and we went for a modern, clean and graphically appealing product to
bring some color and excitement back into the wheel market,” said Kiffmeyer. “I
want the customer to say, ‘I know it’s strong, I know it’s fast, but damn it
looks good.’” Since its Interbike debut Industry Nine has been steadily
ramping up production and distribution. Along with road and BMX wheels, the
company is working on a new line of stems and seatposts.
“We’re thrilled with how well
it’s been received,” said Clint Spiegel, the company’s co-designer and vice
president of its 120-employee parent company Turnamics, an Ashville, North
Carolina, based design and manufacturing shop. Industry Nine shares some
resources with the parent outfit but now has four full-time employees of its
own. Spiegel said he has worked with high-end golf products, tactical
knives, robotics and industrial packaging machinery and has never met with such
a positive initial reception. “The buzz and excitement level in the
industry”—bicycles are his ninth—“have been great.” To find out more
about the company visit its Web site at www.industrynine.net(flash required) or
call them at (800) 404-1775.
Group shot caption: (L to R) John
Kiffmeyer, project manager; Fred Schuldt, production manager; Jeff Baucom,
national sales manager; Clint Spiegel, vice president, Turnamics
Industry Nine Gallery
engineers accustomed to making precision robotics, high-end golf clubs and
medical equipment in a multi-million-dollar manufacturing facility and set them
loose designing bike components? In the case of Industry Nine, a new Asheville, North
Carolina, based components company, those engineers took a modest shot at
reinventing the wheel.
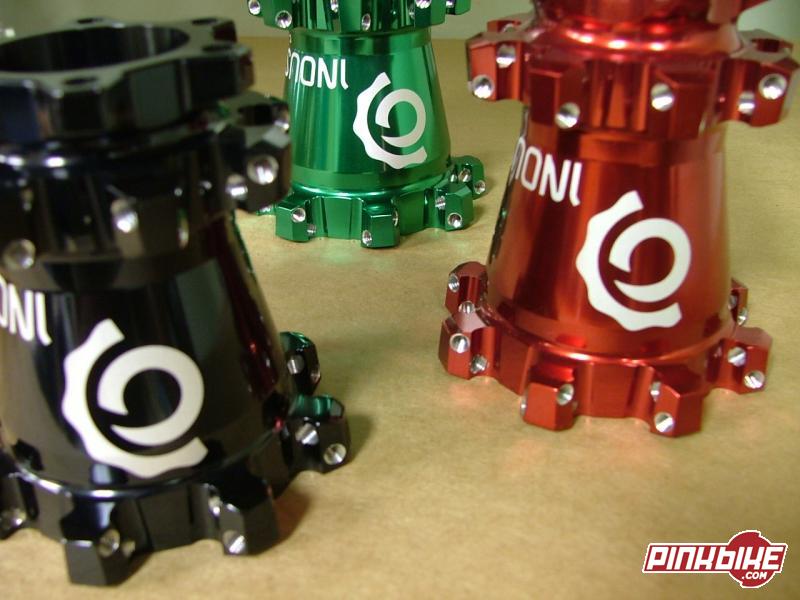
Industry Nine debuted at
Interbike last year with its unique new wheel design featuring an integrated
spoke-and-nipple design machined from a solid rod of 7075 T-6 aluminum. The
spokes thread directly into Industry Nine’s proprietary hub and can be used with
any 32-hole rim. Wheels can be trued with conventional spoke wrenches courtesy
of machined-in wrench flats on the nipple ends.
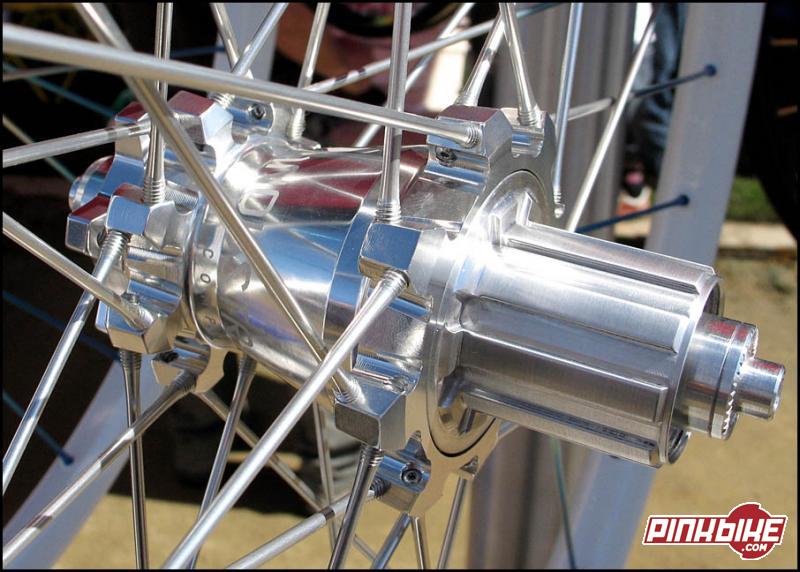
The bottom line for the rider is
fewer parts and—because it’s all aluminum—a lower rotational mass than even some
top competitors. In layman’s terms, that means you accelerate faster. The
process of milling each spoke from a solid bar of extruded aluminum takes about
two minutes per spoke on a quarter-million dollar lathe.
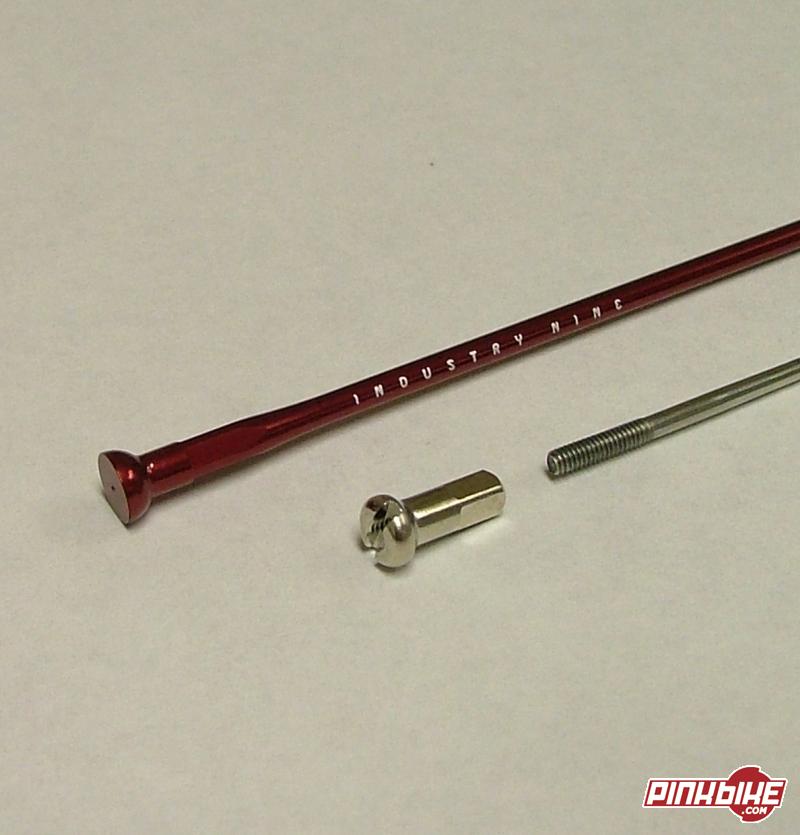
Industry Nine product manager
John Kiffmeyer said that using 32 spokes, laced to your choice of rim in a
tried-and-true two-cross pattern, makes the company’s wheels stronger than
comparably priced wheels that use forged aluminum spokes with a low-spoke-count,
direct-pull lacing pattern. The company offers stock price-point
wheelsets built with DT Swiss hoops in All-Mountain, Enduro, FR/DH, 29er and
Single Speed variations in three standard colors: anodized black, sliver or red.
Road and BMX wheels are in the works.
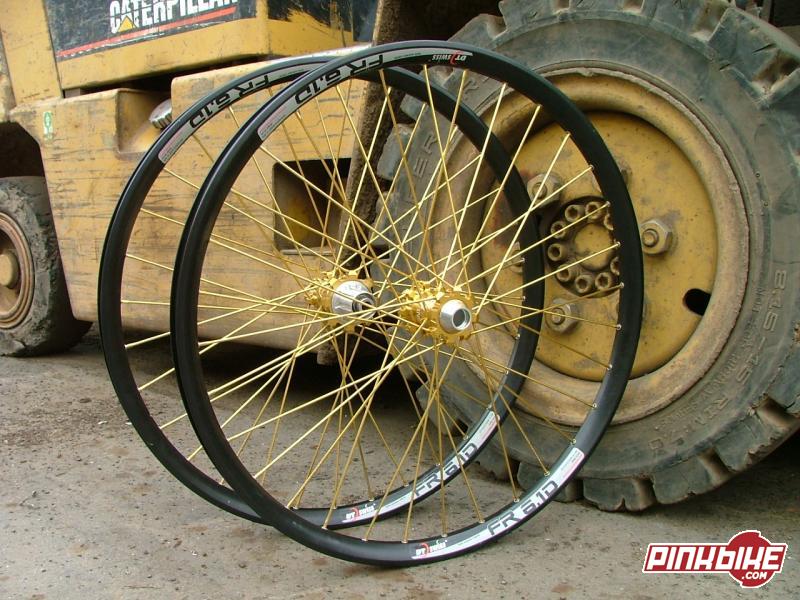
But don’t feel hampered by the
stock offerings—at Industry Nine customization is king. Spoke gauge, length and
spoke and hub color all can be made to order. Industry Nine’s
patent-pending spoke design is just part of the new company’s story. The company
is also waiting on a patent for a new freehub body drive mechanism that it
designed from the ground up. (Kiffmeyer said the company isn’t posting pictures
of the internals until the patent clears, so to see how one in action you have
to buy a rear hub and crack it open.)
The drive mechanism uses three or
six pawls, depending on preference, for engagement every six or three degrees of
rotation, respectively.
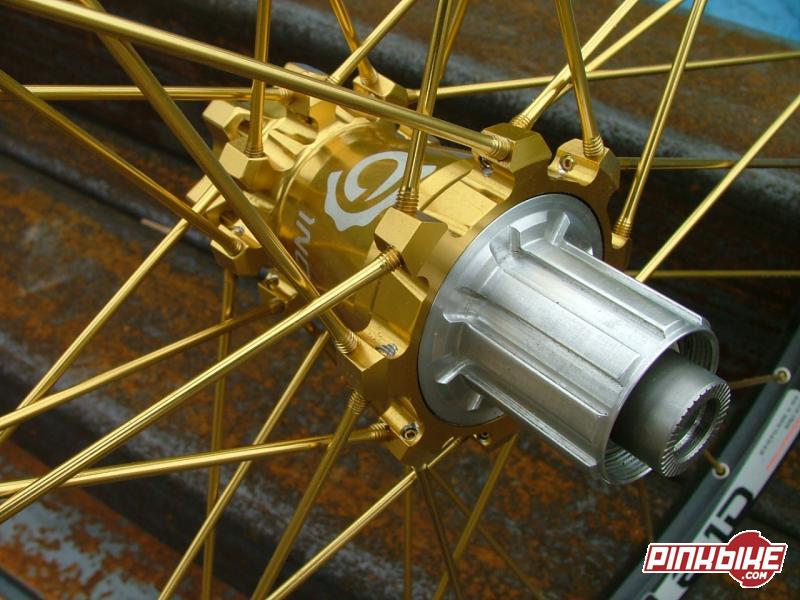
Whether the hub is set up with
the three- or six-pawl option, it is designed to only have three pawls engaged
at any given point. In addition to the hub’s quicker-than- average engagement,
each pawl has three engagement ridges, so there are always nine simultaneous
points of engagement. To ensure that all those tiny engagement points
stand up to even the angriest pedal mashers, the pawls and engagement ring are
cut from A-2 tool-grade steel with a process called Wire EDM (Electrical
Discharge Machining), an electrical erosion process that precision cuts
already-hardened steel to a tolerances within .0001 of an inch. Industry
Nine hubs have hardened stainless steel endcaps and 7075 aluminum hub shells and
axles. Freehub bodies are made from 7068 aluminum, an alloy with tensile
strength 25 percent greater than 7075. Wheelsets come with quick release or
thru-axle options, and the company now offers hub options for Cannondale Lefty
and Maverick fork users.
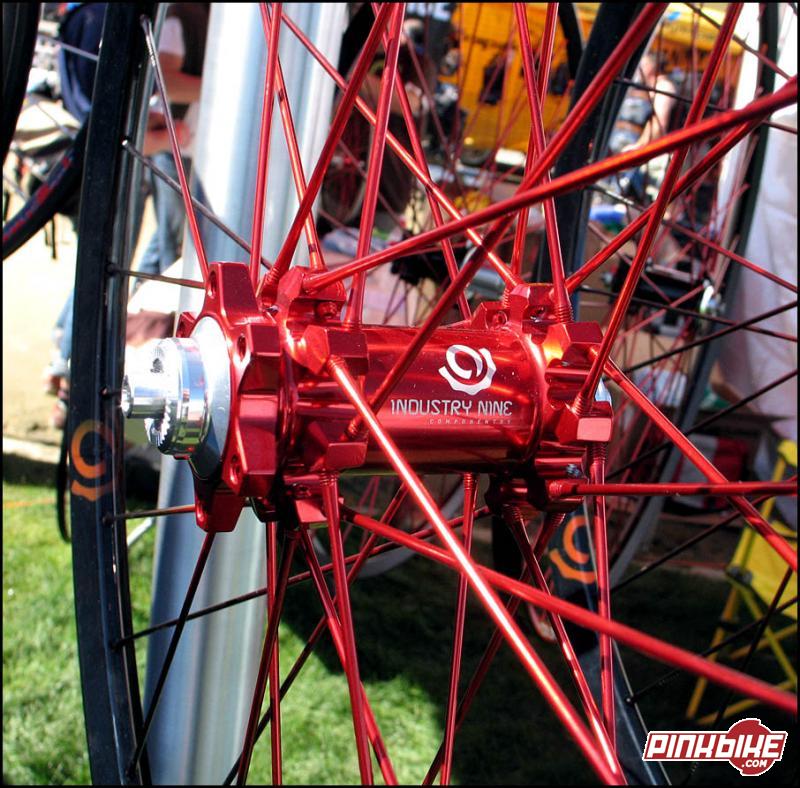
The only components the company
doesn’t fabricate on its own are rims and Japanese-made cartridge bearings—front
hubs get two, rear hubs get four. All that precision machining will set
you back about $850 per wheelset—a price point comparable to other
aluminum-spoked wheelsets but well worth it in terms of performance and the
ever-important “bling” factor. “We’re very aware of how important look
is, and we went for a modern, clean and graphically appealing product to
bring some color and excitement back into the wheel market,” said Kiffmeyer. “I
want the customer to say, ‘I know it’s strong, I know it’s fast, but damn it
looks good.’” Since its Interbike debut Industry Nine has been steadily
ramping up production and distribution. Along with road and BMX wheels, the
company is working on a new line of stems and seatposts.
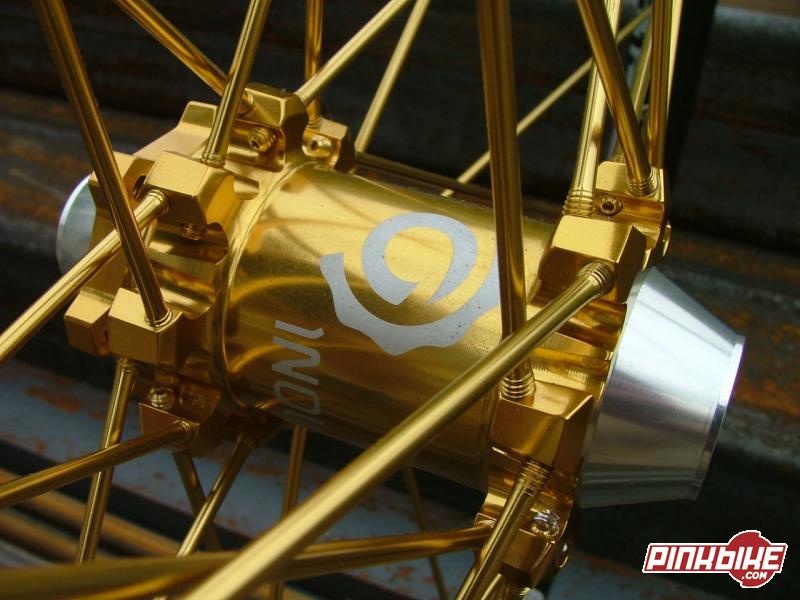
“We’re thrilled with how well
it’s been received,” said Clint Spiegel, the company’s co-designer and vice
president of its 120-employee parent company Turnamics, an Ashville, North
Carolina, based design and manufacturing shop. Industry Nine shares some
resources with the parent outfit but now has four full-time employees of its
own. Spiegel said he has worked with high-end golf products, tactical
knives, robotics and industrial packaging machinery and has never met with such
a positive initial reception. “The buzz and excitement level in the
industry”—bicycles are his ninth—“have been great.” To find out more
about the company visit its Web site at www.industrynine.net(flash required) or
call them at (800) 404-1775.
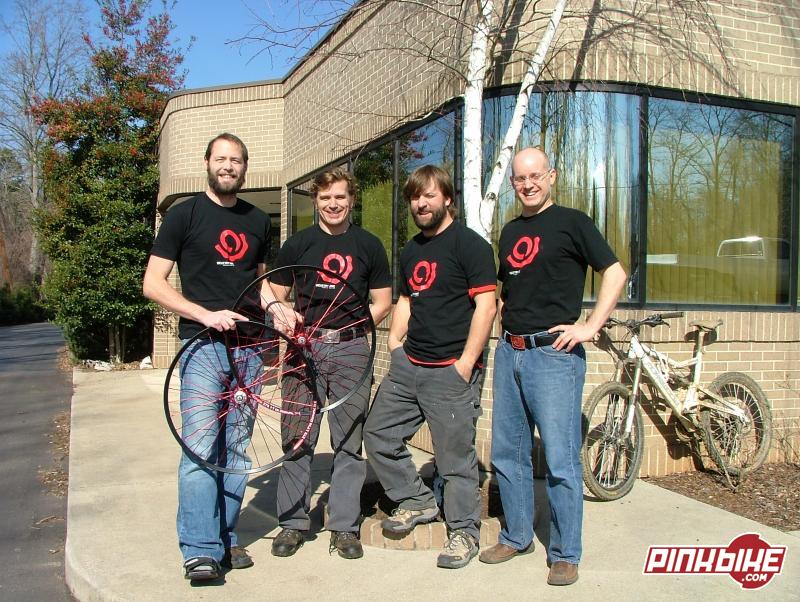
Group shot caption: (L to R) John
Kiffmeyer, project manager; Fred Schuldt, production manager; Jeff Baucom,
national sales manager; Clint Spiegel, vice president, Turnamics
Industry Nine Gallery
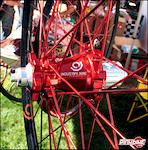
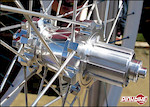
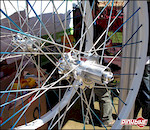
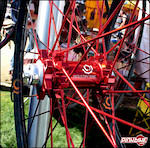
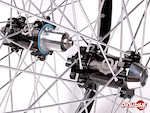
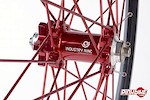
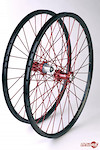
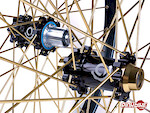
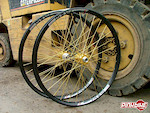
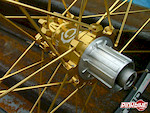
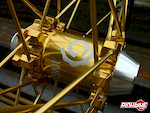
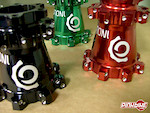
댓글 달기